Improved Feature Line Treatment in
Harpoon
Recent releases of Harpoon have included some important improvements to the
code’s handling of feature lines, which are referred to as “FLs” in the
following article.
Feature lines are used in Harpoon to capture and retain the important
geometric features of a model. These include areas of high curvature and the
boundaries (free edges) of model parts. Harpoon will always attempt to retain
these features during meshing. Target mesh sizes can be defined on different
Fls, or mesh sizes can be specified on the polygons.
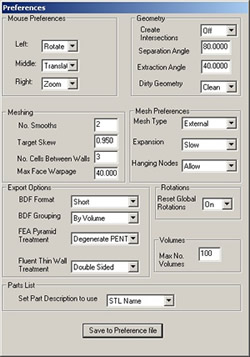 Figure 1 – Harpoon’s Preference dialog, showing the Extraction
Angle used to define FLs associated with geometry features. Click on image for
full-size.
Harpoon defines two types of FLs:
- those described by model features
- those defined by the edges of model parts
For models that consist of more than one part, a separate FL part is created
for each model part. FLs may be merged, renamed, deleted or separated using the
same methods as for polygons -- namely “by Region” or “by
Feature”. A region is defined as all line segments connected to one that
the user selects. This is done by double-clicking on a line segment with the
left mouse button (the number of the segment will appear in the background
window).
Applying the option “Surface > Separate > Line Segment by
Region” on the selected segment results in the original line part being
split into two parts -- one for all line segments connected to the segment
selected, and the other being all segments not connected to it. Alternatively,
applying the option “Surface > Separate > Line Segment by
Feature” on the FL results in multiple new line parts according to the
“Separation Angle” in Harpoon’s preferences.
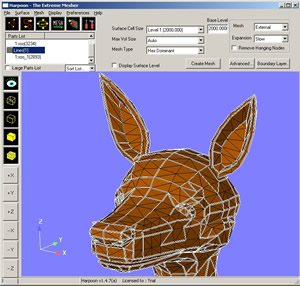 Figure 2a
– Feature Lines for an Extraction Angle of 10 degrees. Click on image for
full-size.
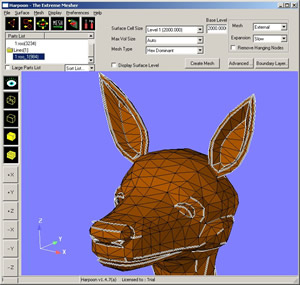 Figure 2b
– Feature Lines for an Extraction Angle of 40 degrees. Click on image
for full-size.
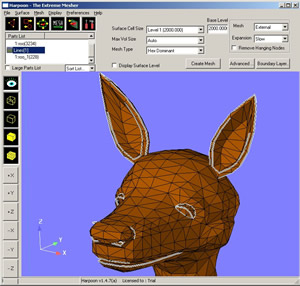 Figure 2c
– Feature Lines for an Extraction Angle of 80 degrees. Click on image for
full-size.
It is important to distinguish between the two angle preferences. “Separation
Angle” is used to separate polygons and line segments based on the included
angles between adjacent polygons or line segments. “Feature Angle” is used to
create FL parts as described above.
By default, Harpoon creates an FL part for each model part to which it is
associated. If a single FL part is desired, the command line option
“-nolineperpart” can be used when starting Harpoon.
FLs on the free edges of model parts may, or may not, be desired. It is
possible to suppress the creation of FLs on the free edges of a model part by
starting Harpoon with the command line option “-noedgeline”. This
option will also invoke the “-nolineperpart” option. FLs will only be
created on part edges if the angles relative to the adjacent model part exceeds
the extraction angle in the preferences. Figures 3a and 3b show
a model with and without FLs on part edges.
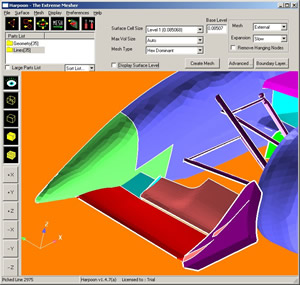 Figure 3a
– Feature Lines resulting from feature extraction and from model part edges
(note line between green and blue parts of race car fuselage) Click on image for
full-size.
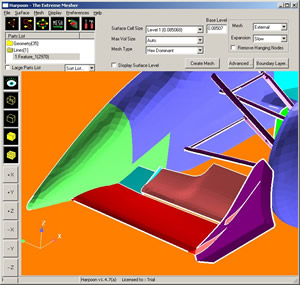 Figure 3b –
Feature Lines resulting only from feature extraction by using “–noedgeline”
command line option when starting Harpoon. Click on image for
full-size.
FLs serve one other important use in Harpoon. If FLs describe closed
circuits, for example around an opening in a model, they can be used to close
the holes. This is especially useful when Harpoon’s hole finding feature - which
in reality looks only for “free edges” (sides of polygons shared by only one
polygon) - results in no holes being found, although they appear in the model.
These are typically not free edges, but openings in thick-walled parts. Since
the edges of these openings are usually sharp, they will appear as FLs.
Separating those describing an opening using the “Surface > Separate >
Line Segment by Region” procedure described above results in a single line
part. The user then selects this line and closes the hole using the normal
hole-closing feature. Figures 4a-c show the sequence of steps
to define and close an opening in a thick-walled part.
Figure
4a – Step 1 of hole closing using FL: extraction of FLs. Note all FL segments on
one FL part. Click on image for full-size.
Figure 4b –
Step 2 of hole closing using FL: Segment on inner circular hole has been
selected. “Separate > Line Segment by Region” used to obtain desired line
part for closure. New FL part (green) has been separated from original FL. Click
on image for full-size.
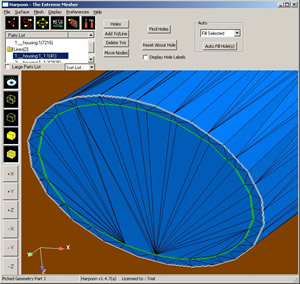 Figure 4c –
Step 3 of hole closing using FL: New FL part is selected then normal hole
filling option has been used to close this hole. Additional facets are added to
adjacent model part. Click on image for full-size.
The information above may be found in Harpoon’s User Guide, viewed through
Harpoon’s “Help” facility. 
|