Harpoon extreme mesher gets teeth into biomechanics research
While military applications and crash simulations have long been hot areas for computational solid mechanics, advanced computer software is bringing biomechanics – with its highly complex structures and morphologies – further into the fold. The use of mechanical analysis techniques in cell biology, the nervous system and even dental implants and fillings is benefiting from timesaving advances in Harpoon, the extreme mesher, developed by Manchester-based, Sharc.
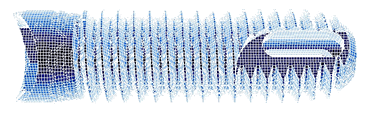
Dr Ronald Sakaguchi, professor of biomaterials and biomechanics and assistant dean for research at Oregon Health and Science University in Portland , studies the mechanics of biomedical devices. His laboratory has both an experimental laboratory and a computational modelling component. These operate hand in hand – experimental techniques are used to develop mechanical properties and general behavioural boundaries for the materials. Those properties are then used in the computational models his team builds. His team’s studies of dental implants and restorations under varying loads help provide guidelines for use by clinicians. Several of his team members use Harpoon daily.
Dental implants are now often considered the treatment of choice by dentists to replace single missing teeth or multiple teeth when a removable partial or full denture is not acceptable to the patient or when substantial tooth structure would need to be removed to accommodate a fixed bridge. Implants are most commonly made from commercially pure titanium or a titanium alloy. The forces placed on implants can be as high as 100 to 150 pounds, so it is important to know the mechanics of how the implants perform when loaded.
Meshing the threads
Creation and analysis of 3D computer models is a critical component for biomedical device research. In the case of finite element analysis (FEA) of threaded dental implants, meshing of the helical threads is challenging. Dr Sakaguchi has not been able to find a software tool that would mesh such geometry reliably. Meshing the root of the threads typically results in tetrahedral elements with poor aspect ratios. Prior to using Harpoon, meshing was done manually, assuming there was access to a CAD file. If not, one of the team would have to reverse engineer the object, requiring several weeks or even months of effort.
“Constructing the model geometry and generating the finite element mesh was very time-consuming,” says Dr Sakaguchi. “A disproportionate amount of time was spent creating the geometry rather than doing the actual analysis and research.”
Dr Sakaguchi says that Harpoon creates complex meshes without any difficulty, the process does not require additional software, and only minimal manual clean-up is needed. This is in stark contrast to other mesh programmes he’s tried. Meshes created by Harpoon also allow flexibility in density, which enables Dr Sakaguchi to solve FEA problems quickly and correctly.
“I can take a SolidWorks CAD file, mesh it in Harpoon, and then solve it for stresses and displacements using an FEA solver, usually MSC.MARC, in minutes, rather than days, weeks or months,” says Dr Sakaguchi.
Condensing the multiple time-consuming processes into three key steps, Dr Sakaguchi and his team are able to more fully explore ’what-if’ scenarios. Through this virtual prototyping, the number of physical prototypes and amount of bench testing can be minimised. This can potentially reduce the number of designs placed into clinical trials, allowing medical and dental device manufacturers to bring improved products to market more quickly. Dr Sakaguchi comments: “Harpoon has really revolutionised the way we approach modelling. Before Harpoon, there were models we wouldn’t even try to build because we knew how long it was going to take to create the mesh. Now we just pass the CAD files through Harpoon and the job is done quickly and easily.”
Dr Sakaguchi and his team have been using Harpoon for a little over nine months and are really impressed with the way it works. They are equally impressed with the support they have received from CEI (the US distributor for Harpoon) and Sharc. “Both CEI and Sharc have been terrific in their ongoing development of the product and their technical support,” says Dr Sakaguchi. “It’s amazing that this product does not require a high-end UNIX workstation. Harpoon runs just fine on a mid-level Windows notebook computer.”
More than a mouthful
Dr Sakaguchi’s research team uses the tools developed for biomedical analysis of dental implants and restorations in other areas as well. He uses the same processes to study the mechanics of vascular stents, which are used to keep diseased blood vessels open.
Dr Sakaguchi explains: “When you start deploying a vascular stent, the behaviour of the stent against the vessel wall is unpredictable. We try to evaluate different parameters and model how the stent will deploy. Through numerical modelling we can easily change the material properties of the stent and the properties of the vessel. Harpoon simplifies creation of the finite element mesh, particularly complex geometries such as vascular stents.”
Another possible area of research is craniofacial development and oral and maxillofacial surgery. “Anatomical CAD models could be easily meshed through Harpoon and then analysed using growth or healing patterns as boundary conditions,” says Dr Sakaguchi. “Anytime we have a CAD database and need a finite element mesh for structural mechanics modelling, Harpoon is the best solution as it simplifies the transition between the two, which in the past has been very tedious.”
Mammoth time saving
“By using Harpoon to bridge between CAD and finite element analysis, I’ve been able to eliminate 90 percent of the time previously spent to build models for research,” adds Dr Sakaguchi. “For example, Harpoon successfully meshed the highly complex helical thread design of a dental implant at our first attempt. The mesh was clean and accurate. This was the first time we were able to analyse a dental implant using the exact dimensions of the finished product provided by the CAD file used the manufacture of the implant. Computational biomechanics benefits tremendously from the speed and accuracy of this mesher.”

|